Ring Wheel & Spider
- tomsenior
- May 3, 2019
- 1 min read
The 312 tooth epicyclic ring-wheel and spider are one of the main points of interest of Strutt's clock, and this section covers the unusual processes needed to manufacture these components.
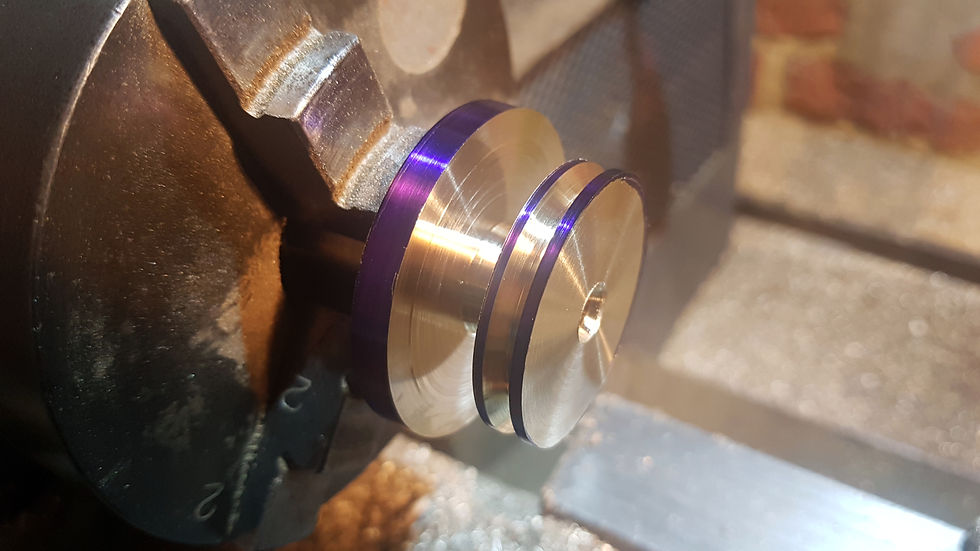
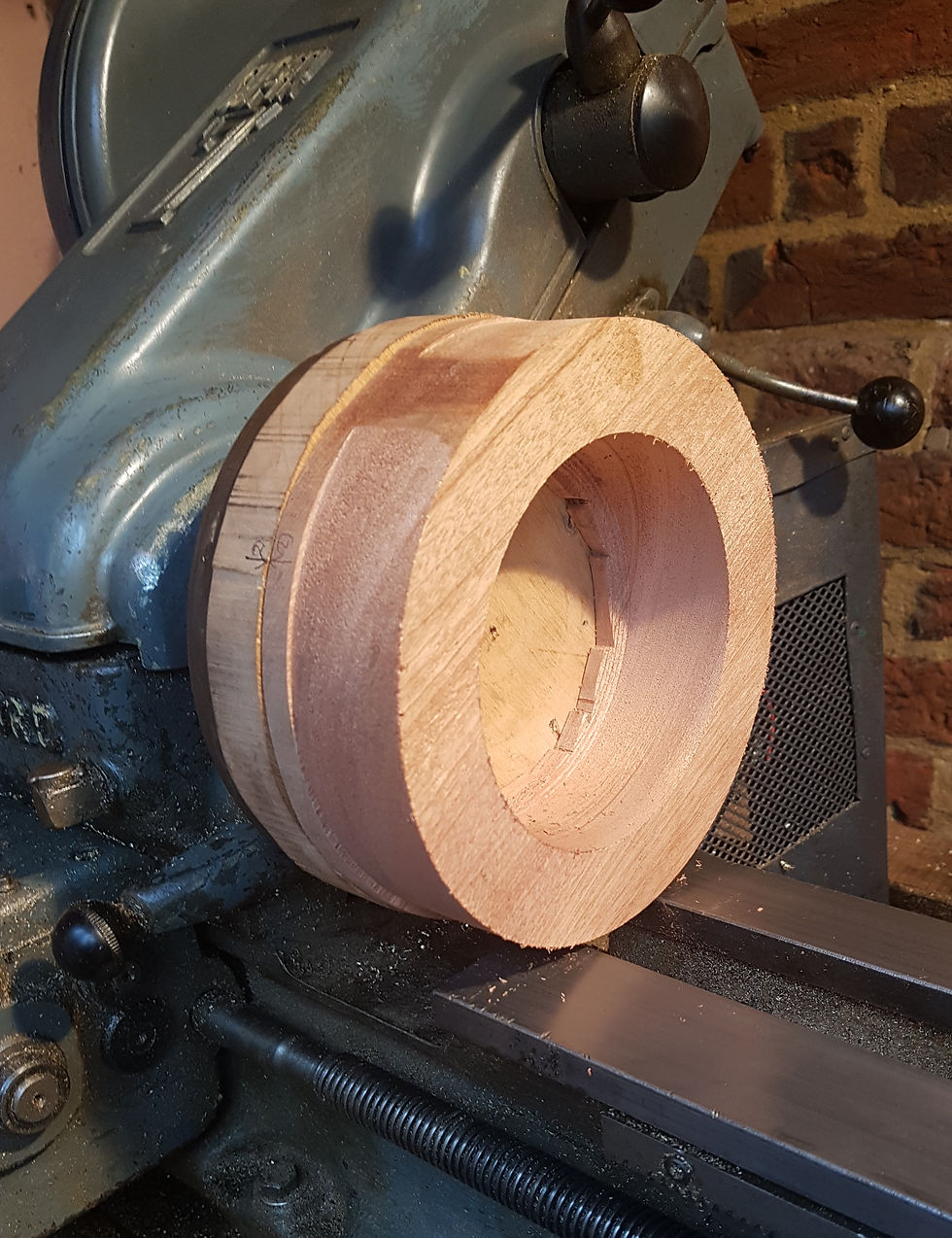


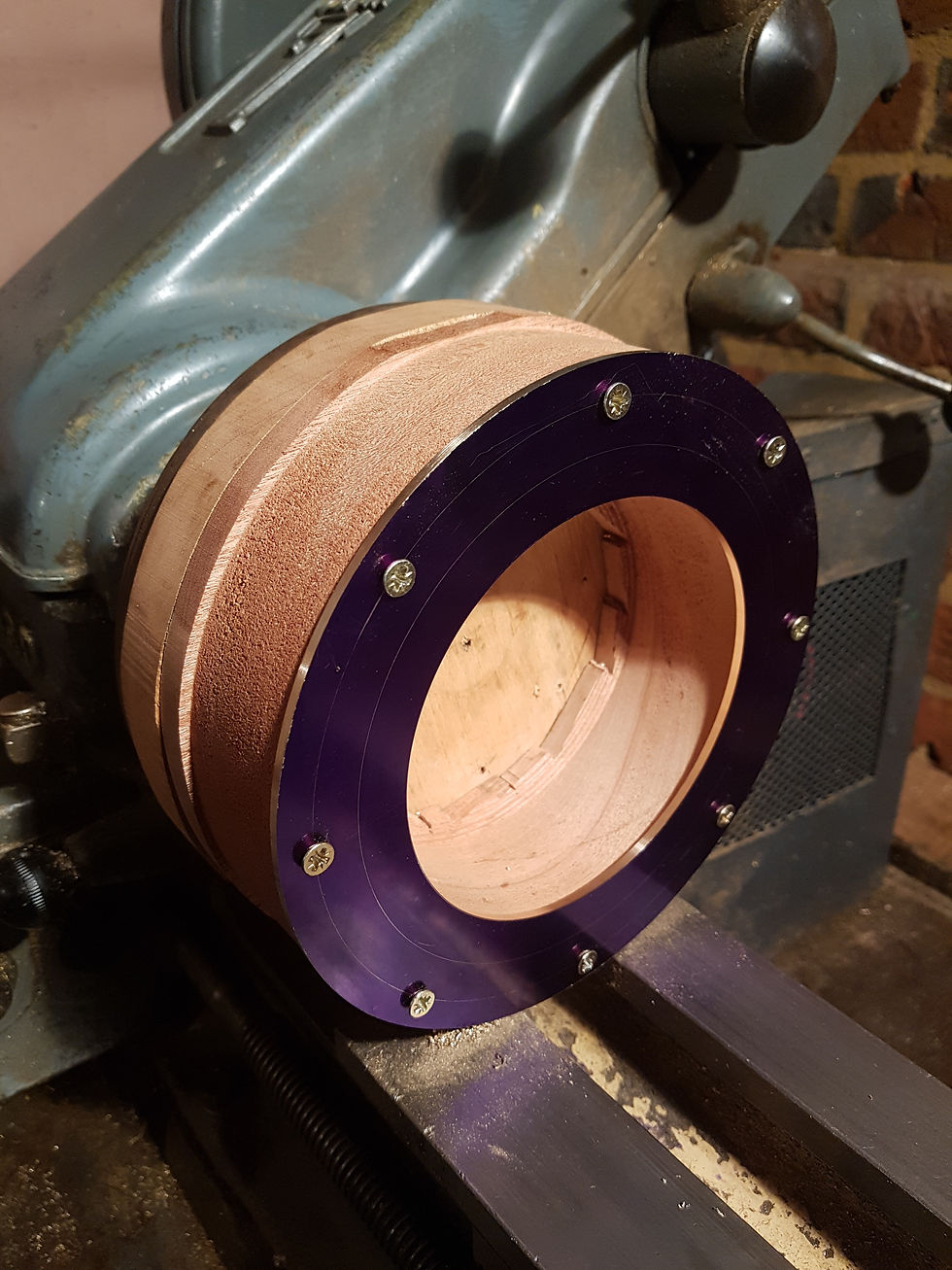
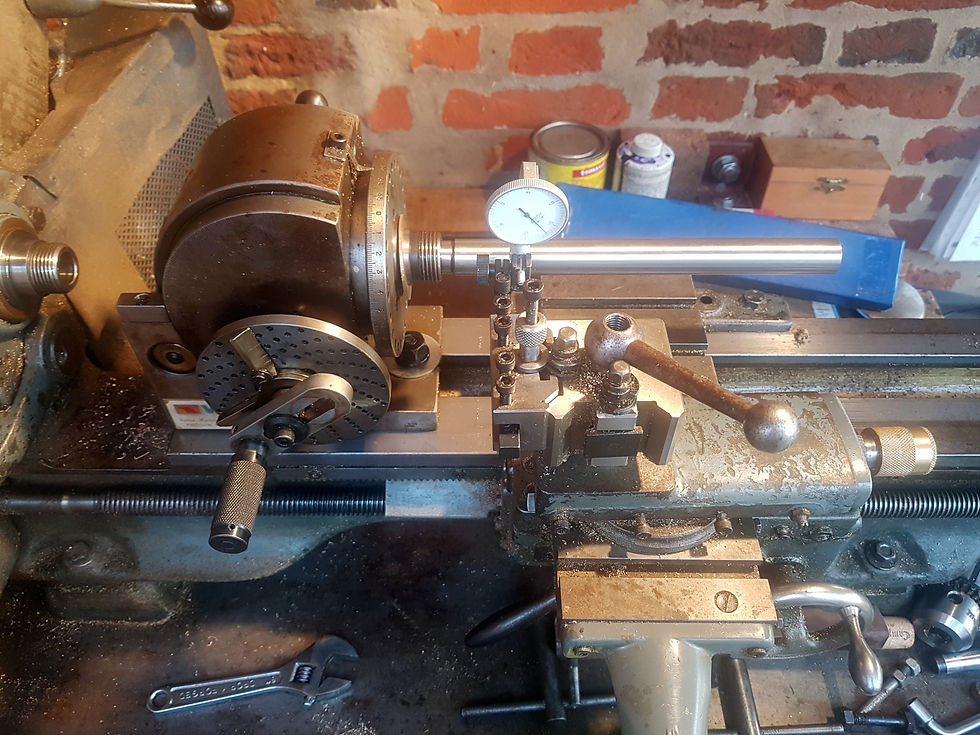
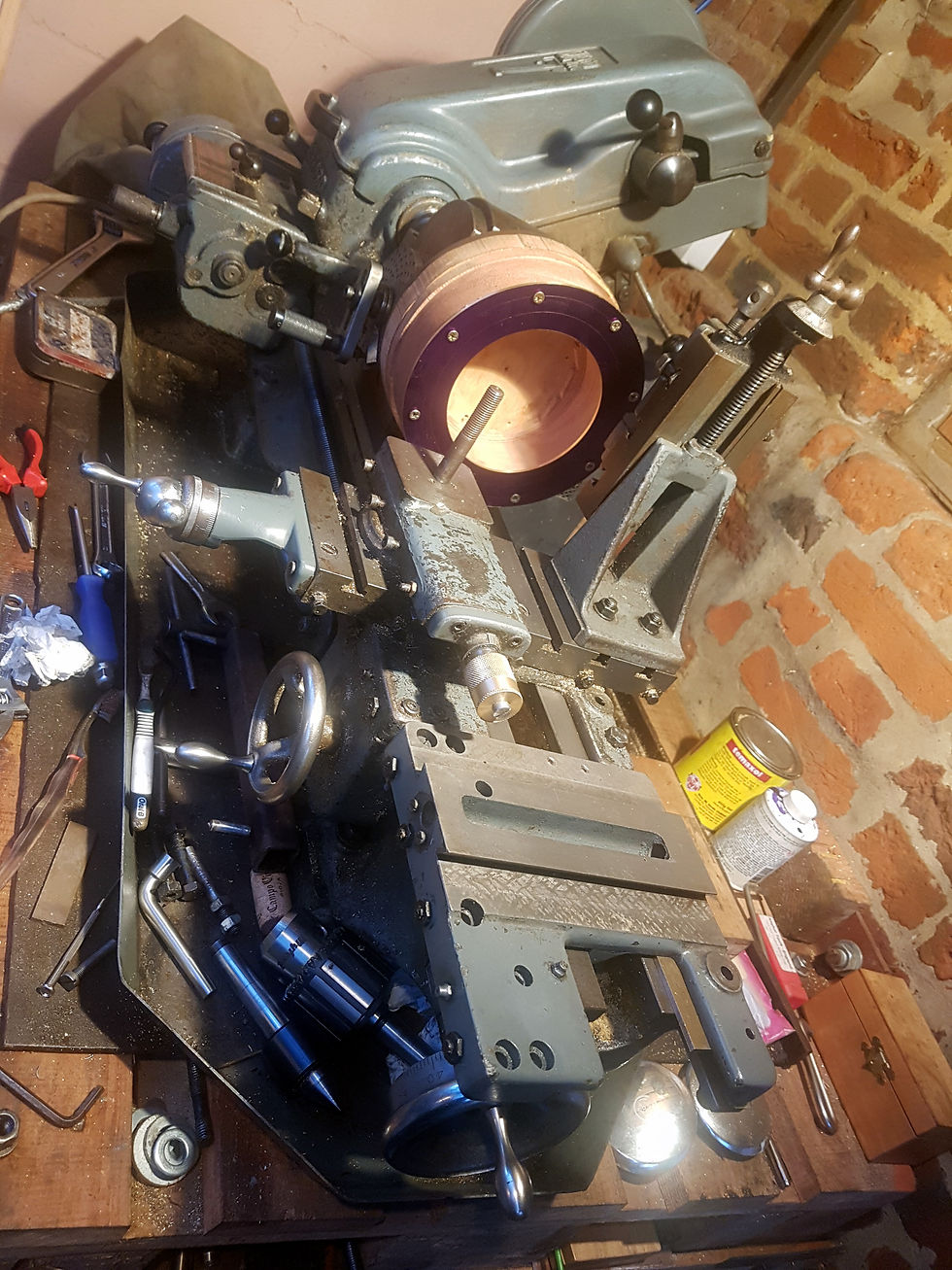





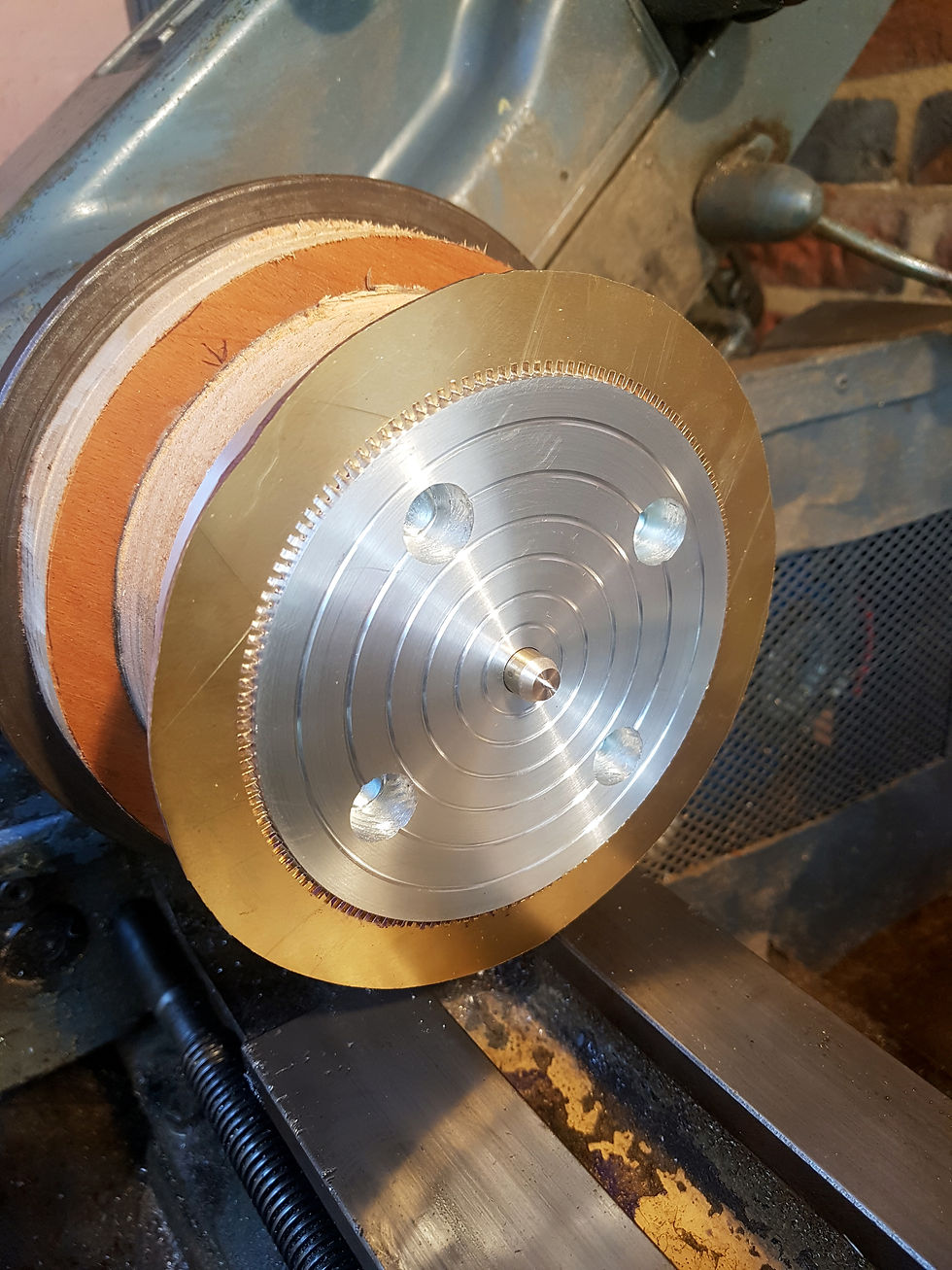


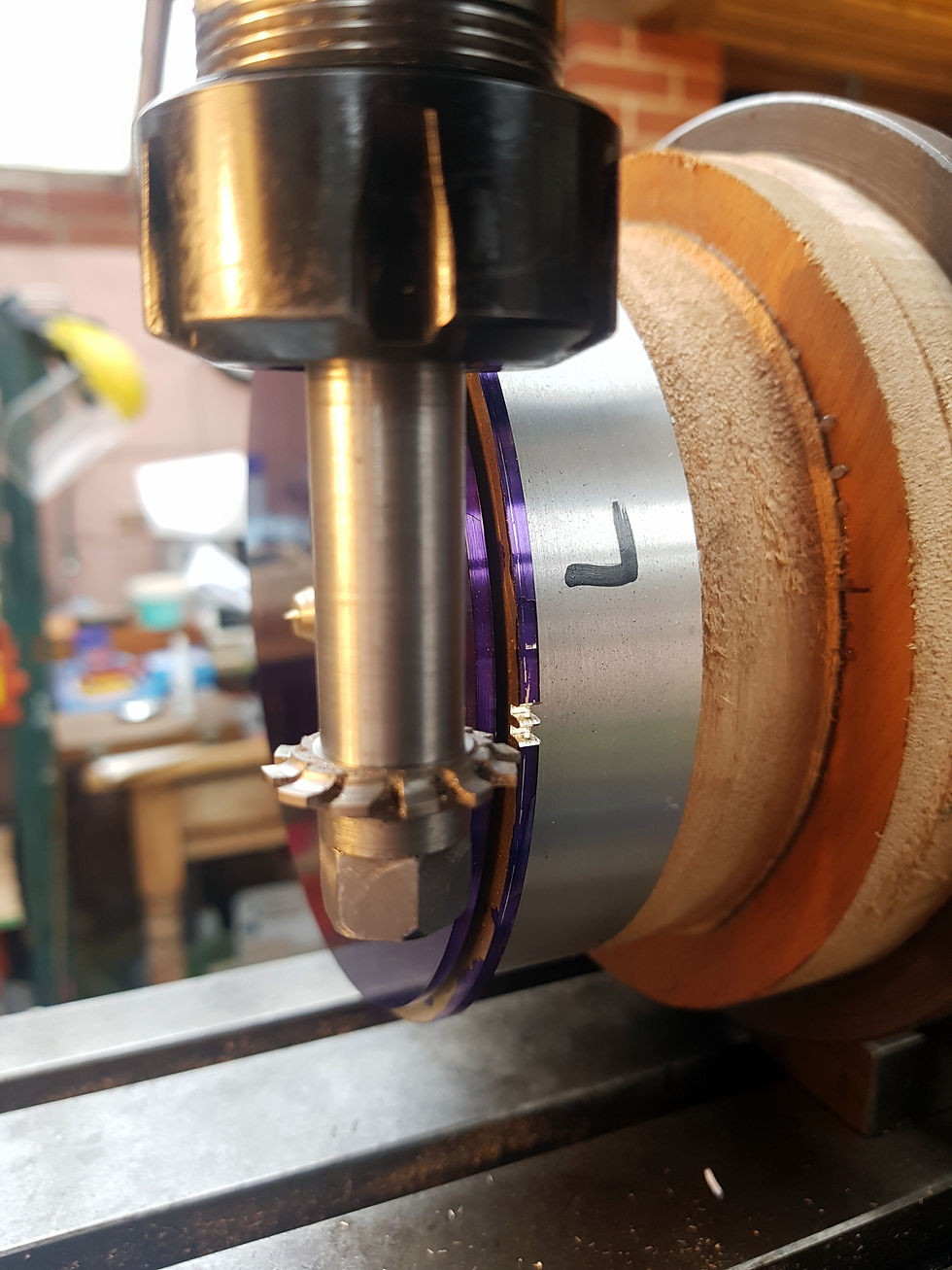
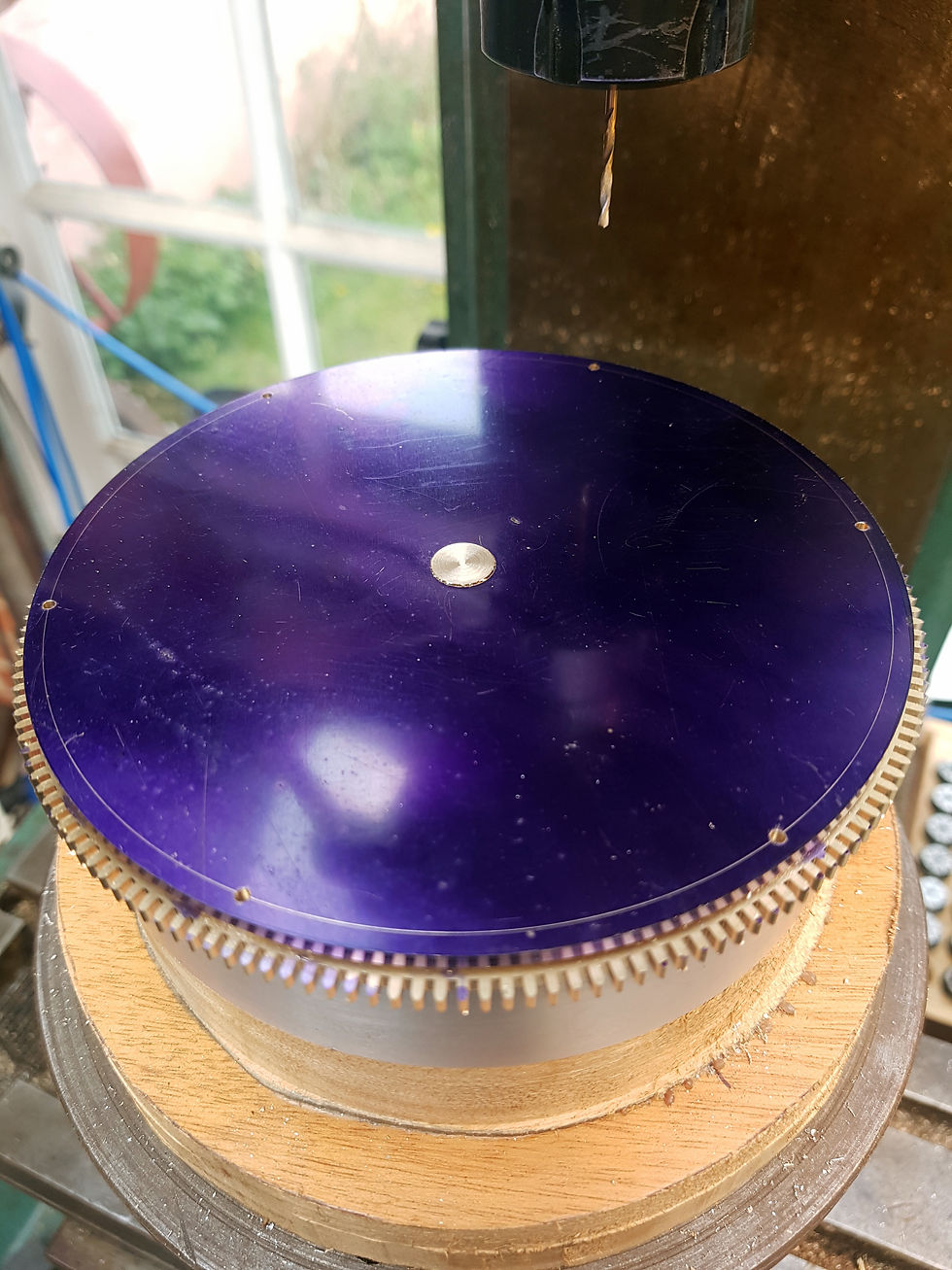
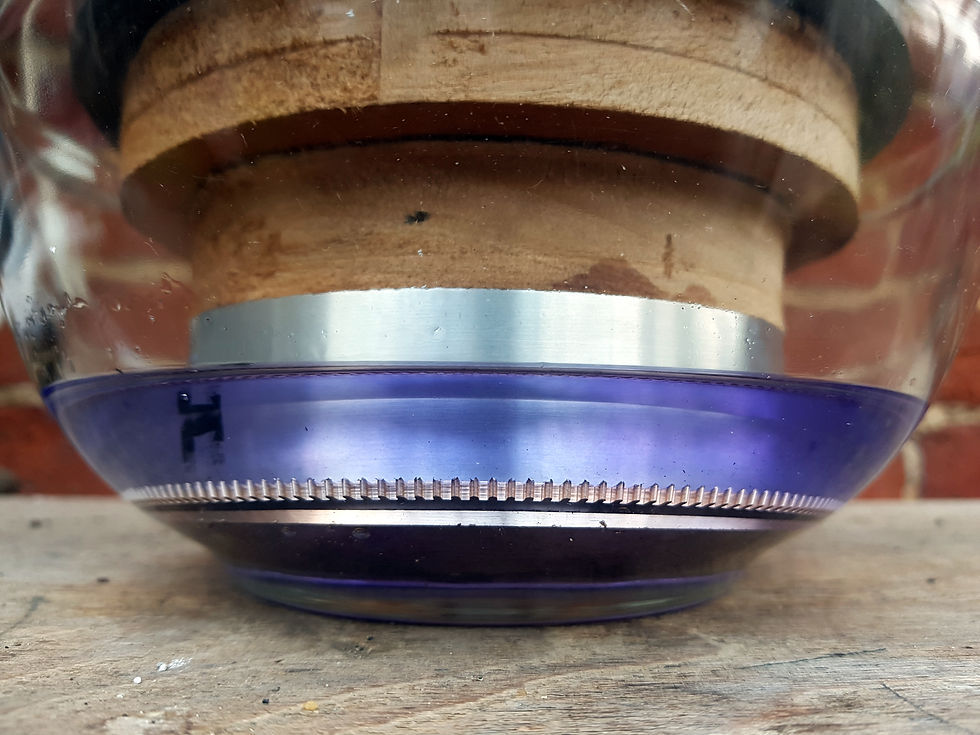






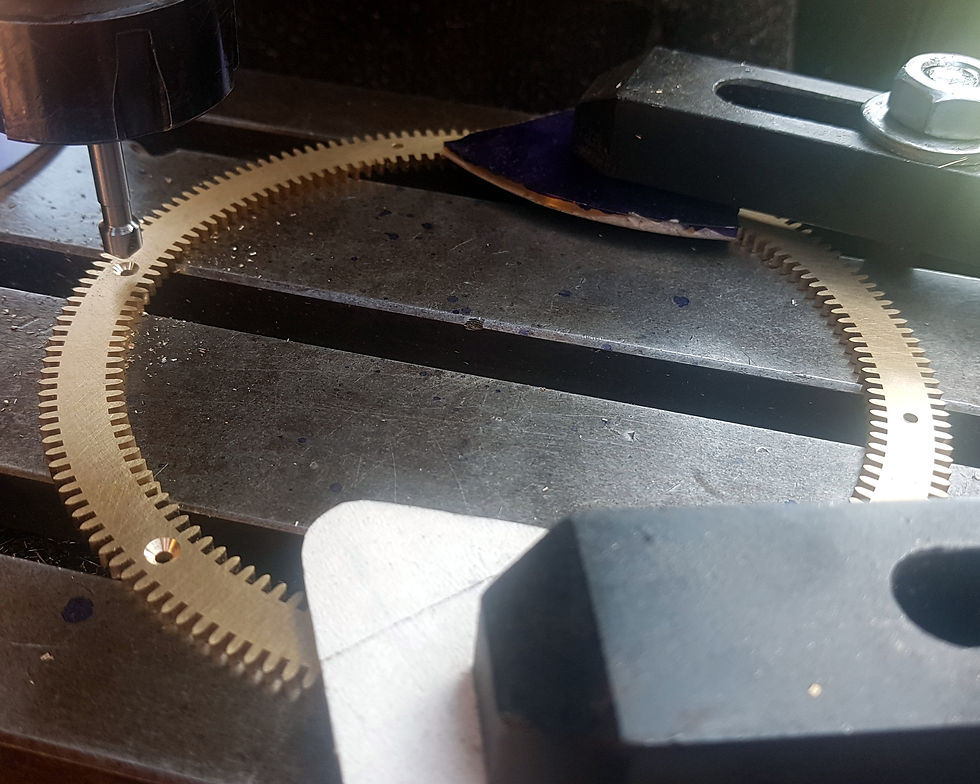

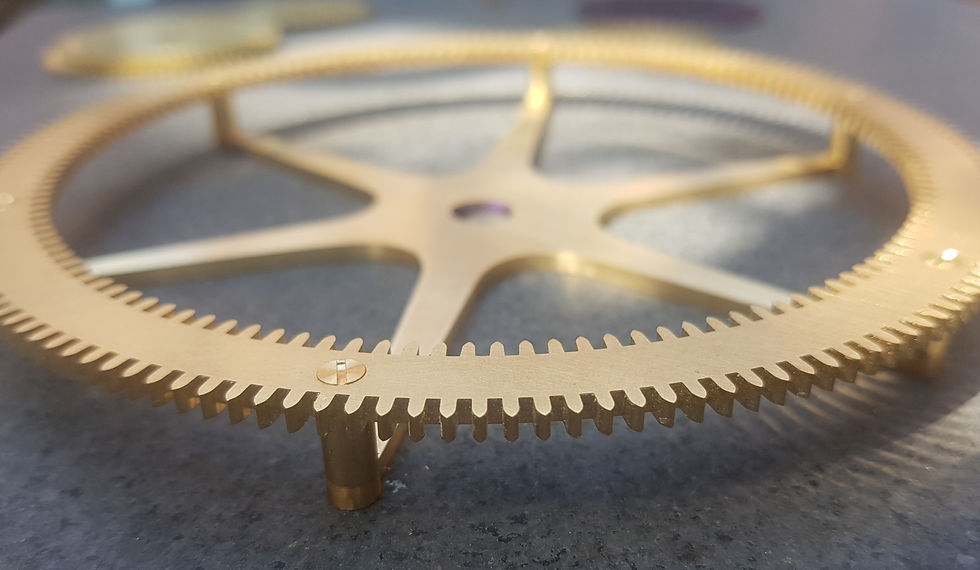
The 312 tooth epicyclic ring-wheel and spider are one of the main points of interest of Strutt's clock, and this section covers the unusual processes needed to manufacture these components.
Comments